Milling is a machining process used to machine various materials such as metal, wood, and plastics. It is also considered one of the most common machining processes available. Milling involves removing material from a workpiece using a rotating cutting tool typically mounted on a spindle—the cutting tool moves along multiple axes, creating the desired shape and dimensions on the workpiece.
There are two main categories of milling, namely vertical and horizontal milling machines, which have individual advantages and applications. Each offers distinct benefits that cater to the specified needs of machinists and engineers, which we will explore to find the best machine for your needs.
Choosing the Right Milling Machine
Both vertical and horizontal milling machines incorporate CNC technology to achieve accuracy. This accuracy is crucial in meeting the exacting standards of today's manufacturing and engineering projects. However, when deciding between horizontal and vertical milling machines, various factors come into play to ensure the optimal choice aligns with the project's specific requirements. Here are several key considerations to guide your decision-making process:
- Workpiece Size and Shape: The size and shape of the workpiece play a crucial role in determining the appropriate milling machine. Horizontal milling is preferred for larger and box-shaped workpieces due to its efficient handling of such components. Conversely, vertical milling shines when dealing with intricate and 3D-shaped components, offering greater precision and versatility in machining operations.
- Production Volume: Consider the production volume requirements of your project. Horizontal mills excel in high-volume production scenarios thanks to their efficiency in rapid material removal and simultaneous cutting capabilities. On the other hand, vertical counterparts are more adaptable for smaller batch sizes and prototyping work, providing meticulous cutting capabilities ideal for intricate designs and limited production runs.
- Machining Complexity: Assess the complexity of the machining tasks involved in your project. Horizontal milling is well-suited for straightforward flat surfaces, making it sufficient for simple machining operations. However, for projects involving intricate shapes, angles, and contours, vertical milling offers greater flexibility and maneuverability, enabling precise machining of complex geometries with ease.
- Accessibility: Consider the spatial constraints and accessibility within your machining environment. Vertical milling machinery boasts space efficiency and is commonly found in machining shops due to its compact design and widespread usage. This accessibility makes vertical mills a convenient choice for many applications, offering ease of access and integration into existing workflows.
- Cost-efficiency: Evaluate the cost-effectiveness of each milling option relative to your project requirements. Vertical milling machines offer cost efficiency and detailed monitoring capabilities, making them ideal for projects demanding intricate precision and meticulous attention to detail. Conversely, horizontal mill machines prioritize speed and durability, making them well-suited for high-volume production environments where efficiency and throughput are paramount.
By thoroughly evaluating these factors, you can determine whether horizontal or vertical milling best meets your project's requirements. This guarantees superior outcomes and streamlined efficiency in your machining endeavors, which is precisely what Ardell Engineering excels at providing.
Horizontal Milling
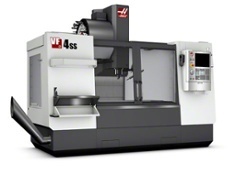
One of the critical strengths of horizontal milling machines is their ability to excel in rapid production. These machines significantly enhance productivity by facilitating multiple cuts simultaneously, making them ideal for high-volume manufacturing environments. Moreover, their design facilitates faster chip removal, which is particularly beneficial for heavy-duty cutting tasks and large workpieces.
Due to the nature of the tasks of horizontal mills, these machines are built to last with their size and durable construction, which enables them to handle larger and heavier materials with minimal risk of damage to the machine.
The horizontal orientation of the spindle plays a crucial role in the efficiency of chip evacuation. These machines ensure smooth machining operations by preventing chip buildup which enhances overall efficiency and surface finish quality.
Ideal for producing flat surfaces, cutting slots, grooves, and keyways, our horizontal mills excel in machining box-shaped parts and components. Their versatile design expands their applicability across various industries, making them an indispensable tool in precision CNC milling.
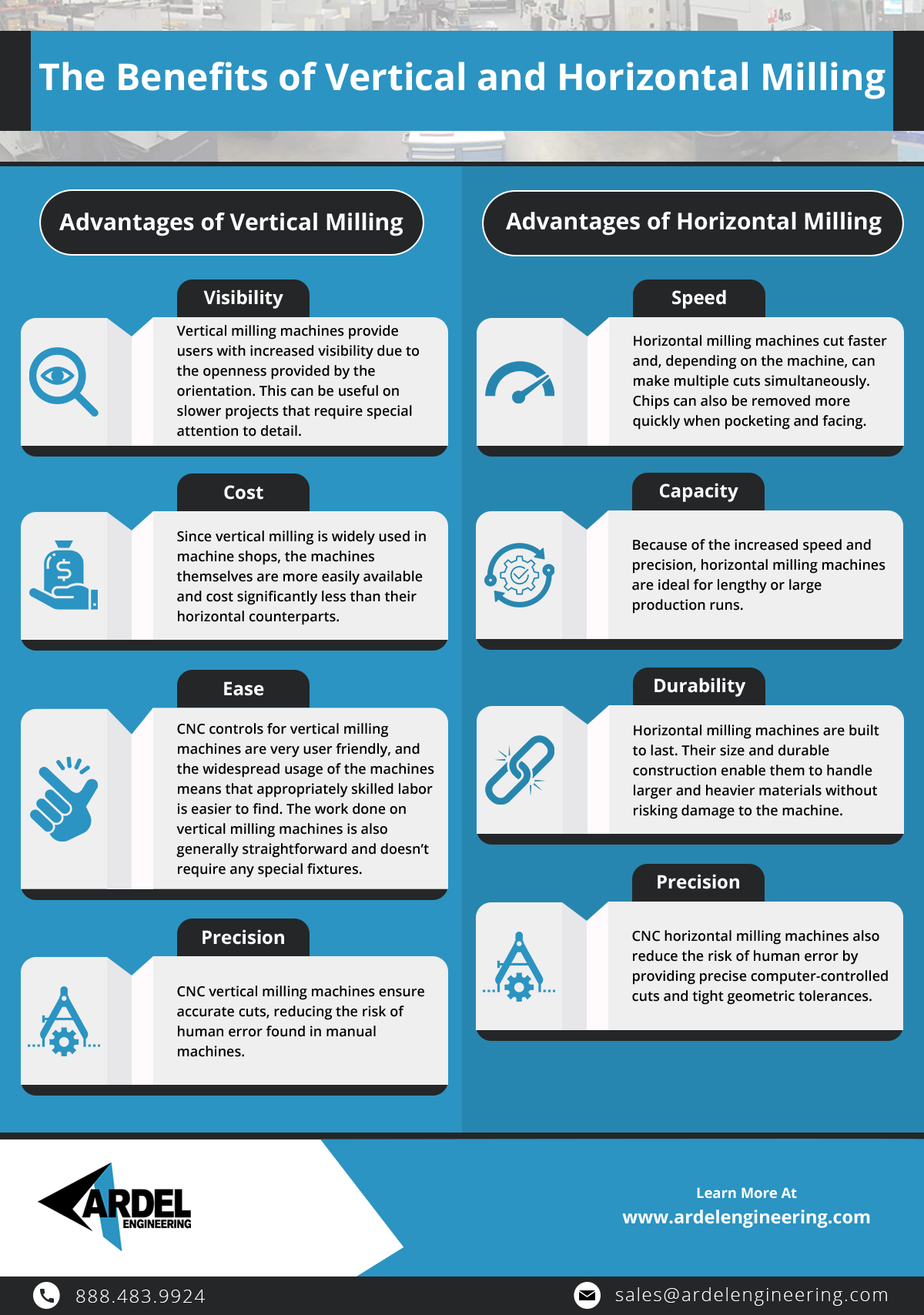
Vertical Milling
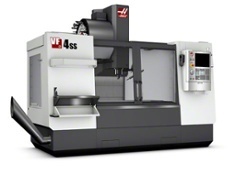
As the name suggests, vertical milling machines feature a vertically oriented spindle mounted on a vertical arbor, enabling material removal in a vertical direction. This vertical orientation grants these machines remarkable versatility and precision. They are capable of handling various cutting tasks like plunge, face, and end milling, which are crucial in machining operations. Enhanced visibility of the machining process ensures meticulous monitoring, which is ideal for projects requiring intricate detail.
Aside from their versatility, vertical mills are known for their space efficiency, making them ubiquitous in machining shops. Their accessibility and precision CNC milling capabilities, equipped with user-friendly Computer Numerical Control (CNC) technology, minimize errors associated with manual operations. This makes them a preferred choice for detailed applications compared to horizontal counterparts.
Vertical mills play a pivotal role in 3D machining, excelling in creating intricate shapes with unparalleled precision. Particularly adept at drilling and boring operations, they ensure precise dimensions and geometries within the workpiece, underscoring their indispensable role in modern manufacturing processes.
Find Your Milling Needs at Ardell Engineering
At Ardel Engineering, precision CNC milling and turning are not just our areas of expertise; they are our passion. With a fleet of 23 cutting-edge milling centers at our disposal, we have the equipment and capacity to turn your designs into reality with unparalleled precision and efficiency. But our services don't stop at milling. We offer a comprehensive range of machining services to ensure every aspect of your project is handled seamlessly, from grinding and honing to deburring, part fabrication, sawing, and drilling.
What sets us apart is our commitment to excellence and attention to detail. We go above and beyond to meet and exceed your expectations, delivering exceptional results every time. And if your project requires additional services, our extensive network of trusted partners is standing by to provide everything from painting and plating to welding and heat treatment.
When it comes to precision machining, trust the experts at Ardel Engineering to bring your vision to life with unmatched quality and craftsmanship. Let us be your partner in success.
For further insights into vertical and horizontal milling capabilities or to explore how our array of machining and value-added services can elevate your project, we invite you to reach out for a quote or to initiate contact with us.