For years now we have been monitoring the progress of 3D printing, AKA additive manufacturing, as the technologies, techniques, and interest in it advance.
As industries slowly begin to embrace this new technology, we will explore some of the challenges faced with integrating this new capability.
Prototyping and Machining Challenges
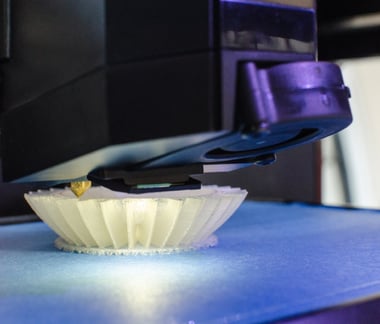
In the machine shop, 3D printing technology opens up the possibility of a new level of designing and prototyping. It allows the user to choose from a wide variety of materials including plastics, metals, and alloys. Although it sounds like the perfect opportunity to advance manufacturing, there are certain factors that must be considered before ruling out traditional machining practices in favor of 3D printing.
In full scale manufacturing, each project must consider cost, time, and quality, with quality being the highest and final goal. Additive manufacturing is the ideal solution for certain types of components but not for all. Prototype fabrication suits 3D printing’s capabilities because designs can be evaluated, modified, and tested in a shorter time that doesn’t require special tooling or machine set up. The ability to change the design is easy, and in some cases, could be too easy making the prototype design process too time consuming and delayed.
Depending on the material and the size, the final products produced through 3D printing may not have the structural integrity and perfection achieved through traditional machining processes. When secondary operations are required, the time and cost required may not benefit the use of the 3D printer. While printers are gaining the capabilities to make larger sized parts, the cost of these machines adds to the cost of the final products as well.

Manufacturing Challenges
Designing for manufacturability can also be a challenge when using 3D printing. In large scale production runs, 3D printing isn’t a viable option over traditional manufacturing. 3D printing of a prototype must take into account the final production process during the design step.
If a component can be fabricated through 3D printing but the same results cannot be accomplished when the part goes into production, then the project is a failure. This is why designers and engineers must consider all aspects of the project.
Time is also a major challenge of 3D printing. At this point the time and cost required to make one part may not be sustainable for a full fabrication project. 3D printing is not a substitute for precision machining centers and machinery that produce high quality products in a timely manner.
Regulatory No-Man’s-Land
As 3D printed products enter the mainstream markets, the issue regarding regulations arises. Since every product can be different, there aren’t any regulations in place for manufacturers to follow. U.S. regulators who are responsible for products entering the market have a difficult time determining how to test products and explaining what requirements manufacturers need to meet.
This is especially important for products used in safety critical applications where 3D products must prove they are as safe as those products made through conventional manufacturing.
The testing and certification processes for 3D printed products are still a work-in-progress. Regulators are struggling with determining how the products and the materials will behave over time and the consistency of the quality. Manufacturing must find a way to monitor the process, materials, and regulators.
3D printing is a valuable tool and integration into the machine shop will become more widespread in the future. Using this technology to its fullest will benefit designers and manufacturing engineers and become a valuable resource to all manufacturers. As time goes on, learning and exploring the 3D printing process will help us overcome today’s challenges and continue to advance manufacturing capabilities.